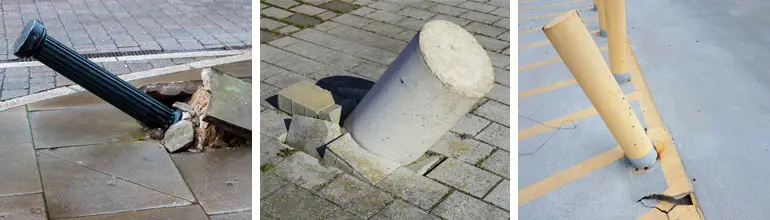
With a variety of bollards available, it can be useful to understand the different types of bollard and the applications to which they are best suited. We have created a handy guide to help you identify the right kind of protection for your facility.
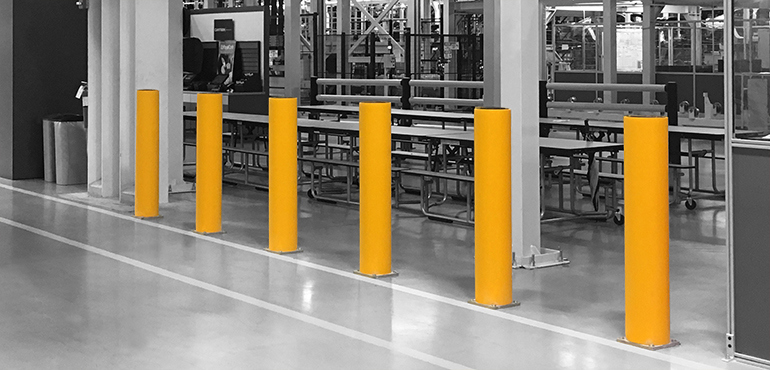
Jump ahead to the section that is relevant to you:
- Understanding the different types of bollards
- Bollard materials: iron, steel, concrete and polymer
- How concrete, steel and polymer bollards handle impacts
- Replacing bollards: How often do you need a new bollard
- The cost of concrete, steel and polymer bollards
1. Understanding the different types of bollards
The various types of bollards provide different levels of protection that are suited to specific situations. These include:
Traffic bollards
Traffic bollards are often used to segregate lines of traffic, especially around roadworks or other types of construction work. Highly visible and often temporary, these bollards can help guide drivers towards designated lanes.
Pedestrian bollards
Pedestrian bollards are used to designate clear areas that are for foot traffic only. These bollards are often placed in areas where pedestrians come into close contact with busy lines of traffic or other possible dangers.
Security bollards
Security bollards function in much the same way as traffic bollards, by segregating traffic from pedestrians. However, they are reinforced and often provide a greater level of protection in the event of a vehicle collision.
Heavy-duty ‘ram raid’ bollards
Performing a similar function to security bollards, these heavy-duty versions are made specifically to prevent vehicles from causing damage or gaining access to highly valuable or secure locations. These can often be found lining the pavement in front of banks, jewellery stores, shopping centres, etc.
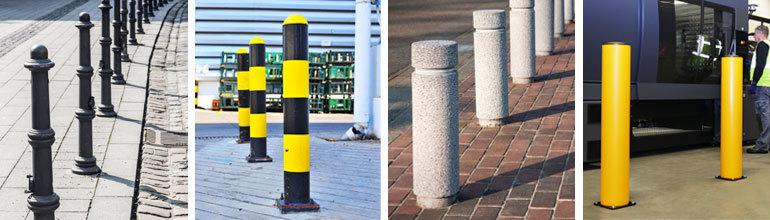
2. Bollard materials: iron, steel, concrete and polymer
Bollards can be made from a variety of materials, with some better suited to certain applications than others.
Iron bollards
Traditional bollards were often made with cast iron. This robust and durable material made them a practical choice, while also allowing for more decorative designs than steel or concrete bollards. The bollards are occasionally a cast iron cover over a steel or concrete post.
Steel bollards
Steel safety bollards can refer to a variety of stainless-steel uprights and metal posts. They often provide protection from vehicles in addition to segregating walkways and prohibiting vehicle access. They are weather-resistant, which makes them useful for long-term outdoor use. Some of these bollards feature a concrete core.
Temporary steel bollards can be removed or lowered to allow access (telescopic bollards), while others are a permanent fixture. Permanent steel bollards tend to be bolted to the floor or secured with concrete.
Concrete bollards
Concrete bollards tend to be found outdoors. They usually take the form of large concrete blocks. They provide robust protection from impacts involving vehicles and are often found in public places with a high volume of pedestrians as a means of protection in the event of traffic accidents or terrorist attacks.
Polymer bollards
Polymer bollards are a more lightweight and flexible alternative to the solid structures of steel and concrete bollards. The polymer plastic material offers a flexibility that isn’t possible with steel or concrete, this allows the bollard to bend on impact and return to its original shape.
These are ideal for providing protection from industrial vehicles, such as forklift trucks. Alternatively, they can provide protection in areas where road vehicles (cars, lorries, etc.) are moving at slow speeds, such as car parks, airports and loading docks or bays. These are often permeant fixtures though removeable options are available.
Standard bollards and heavy-duty bollards
Regardless of the material they are made from, bollards usually come in two different varieties.
Standard bollards
This refers to bollards that are expected to handle smaller-scale impacts, such as those found in car parks. As the speeds of nearby vehicles are likely to be slower, the force of impact on the bollard will be much smaller. Therefore, standard bollards should hold up to this sort of incident with only minor scrapes or scuffs to the surface.
Heavy-duty bollards
As the name suggests, these types of bollard are used more frequently in areas where vehicle impacts are likely to have more force behind them, either as a result of increased speed or weight.
Industrial settings like factories or warehouses use materials handling vehicles such as forklift trucks and side-loaders. These types of vehicle are denser than cars, with much more weight behind them. In the event of an impact, they are likely to do more damage even at slow speeds. Heavy-duty bollards provide a more robust level of protection against the extreme forces of such impacts.
If you’re looking for effective and affordable bollard protection, A-SAFE polymer bollards provide robust, long-lasting defence in busy industrial settings. To find out more about how they work, speak to a member of the A-SAFE team.
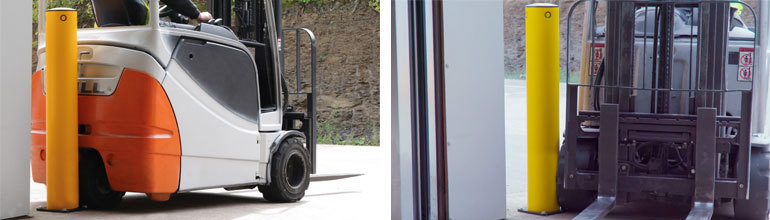
3. How concrete, steel and polymer bollards handle impacts
All bollards are designed to handle impacts; however, their performance and the forces they can withstand varies substantially according to the material they are made from.
Steel bollards
Steel is possibly the most common type of bollard protection, though they are not always the best choice. It depends on the location and the types of impact they could face.
While steel bollards do provide substantial protection – especially against cars and other motor vehicles – they are often a single-use safety product. Once a steel bollard has been struck by a vehicle, depending on the size of the force, it is likely that the bollard will need replacing. The impact will destroy the bollard and possibly the footings that the bollard sits in, as the force of the impact pulls the bollard from its foundations. This would mean a completely new bollard would need to be sourced and installed. It is also highly likely that the concrete base would also need to be repaired or replaced.
Concrete bollards
In many cases, concrete bollards can provide an incredibly high level of protection. Bumps and knocks from vehicles could cause very minor signs of wear.
Therefore, they are often used in situations that demand collision protection from high-speed or incredibly heavy forces. The dense nature of a concrete bollard can often provide more robust defence than a steel bollard.
Concrete bollards can withstand significant impacts but, as with steel, they can be destroyed if the force placed on them is significant. They are also incredibly heavy and often bulky; this makes them unsuitable for indoor use and in instances where safety system configurations may need to be adjusted and reorganised regularly.
Polymer bollards
Polymer bollards are designed to handle impacts of specific weights and speeds. This makes them ideal for use in industrial and workplace settings. The flexible design allows them to absorb and disperse the force of an impact from a variety of vehicles. Unlike their rigid concrete or steel counterparts, polymer barriers are also designed to recover from an impact, eliminating the need for repairs or replacements.
Their robust nature means they can handle heavy duty vehicles, such as forklift trucks and other materials handling vehicles operating at low speeds, or lighter vehicles, such as cars and vans, going slightly faster in locations like car parks and airports.
Polymer provides a resilient yet flexible bollard structure. This means when the bollard is hit, it can flex with the impact to help absorb the force without breaking or causing damage to the footings.
Bollard protection is incredibly important at industrial or warehousing sites with high volumes of traffic. Their function is to protect people and stock, but also machinery and infrastructure. Our flexible polymer bollards are an ideal solution, as they are purpose-designed to withstand impacts from industrial vehicles. Contact us to see how our bollards can make your facility safer.
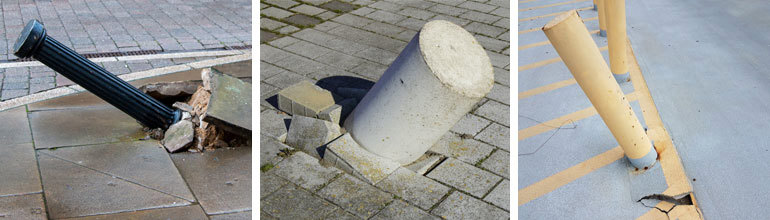
4. Replacing bollards: How often do you need a new bollard?
How often you replace a damaged bollard depends on several factors, such as the frequency of on-site accidents as well as the strength and force of the impacts.
Steel bollards
Steel safety bollards will need to be replaced after a collision. If an impact is small enough in speed and weight, it is possible that the bollard will only suffer superficial damage. However, in most cases, once a steel bollard has been hit, the structural integrity will have been compromised. While the bollard may still be standing, it is highly likely that it will not be able to defend against a similar sized impact in the future. This would mean that whatever it is protecting would still be vulnerable to impacts.
In addition to this, they require a lot of upkeep. If these bollards are being used outdoors or exposed to the elements, it is highly likely that they will start to rust. In busy sites with lots of vehicles, scuffs and scrapes to safety systems are common. With steel protection, these minor faults can create a breeding ground for bacteria and dirt, which is not ideal in facilities that deal with food or medical supplies. Minor scrapes and rust can also start to dull the look of the bollard. This makes it harder for vehicle drivers to spot, and increases the likelihood on accidents.
Concrete bollards
Concrete bollards can often withstand a greater force than steel bollards – especially in the case of large, ram raid bollards. However, standard concrete bollards still share many of the same vulnerabilities as steel. A single impact, if large enough, could break the concrete or damage the steel core inside. This would render the bollard less effective in the event of another impact.
Furthermore, concrete bollards are usually cemented to the ground and their footings can be substantially weakened in the event of an impact. This would potentially mean that the surrounding floor area would need replacing too.
Polymer bollards
Polymer bollards are designed to withstand multiple impacts, which means they should last longer than other types of bollard in busy environments. They are designed to absorb and disperse the energy of the impact so the bollard and its footings can remain intact.
They are created to handle specific weights and forces, so damage can occur if they are hit by larger vehicles or at higher speeds than their specification. However, they are much quicker and easier to replace than other types on bollard, Moreover, most polymer barriers have highly-visible designs that make it easier for drivers and machine operators to see them and avoid any collisions.
Finding the right protection for your site is one thing but being able to trust that it provides long-term security is another. A-SAFE polymer bollards are designed to handle repeated impacts and still return to their original shape and continue providing robust protection. To find out more about the benefits of polymer bollards compared to traditional steel and concrete, speak to a member of our team.
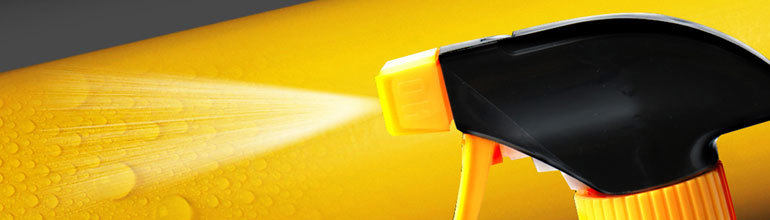
5. The cost of concrete, steel and polymer bollards
Can you really put a price on safety? The practicalities of running a business mean that cost is often an essential factor in choosing safety infrastructure. Therefore, it is worth considering the real and long-term costs of investing in one type of bollard over another.
Steel bollards
The upfront cost of investing in steel safety bollards can be minor; however, it is worth considering not just the initial purchase, but any continued investment required. This includes paying to replace a steel bollard once it has been hit, as well as potentially making costly repairs to the ground if the bollard’s footings are destroyed in a collision.
As mentioned above, steel also requires a lot of upkeep. It’s important to ensure that your steel safety systems do not show too many signs of wear and tear that could eventually lead to rust. Anti-rust treatments and procedures can be costly and time-consuming.
Your safety bollards should be highly visible to drivers, machine operators and pedestrians alike. To ensure they are seen, they will need painting initially and repainting at regular intervals. At large facilities with a lot of safety systems, the cost of that maintenance could be substantial. Again, the upkeep for this would also need factoring into the cost, as scuffs and scrapes will dull the paintwork, reducing the bollards’ visibility, which could cause more site accidents.
Concrete bollards
Similarly, concrete bollards require a comparable level of maintenance to steel. While they are not susceptible to rust, they will need repainting to ensure they are always visible, and this preservation is ongoing.
In addition, concrete bollards will need replacing if destroyed by large impacts. They may also suffer similar levels of damage to the surrounding floor area if the footings are ripped up during a collision.
These costs all add up but might not necessarily be obvious when initially purchasing concrete bollards, so it’s best to evaluate the types and frequency of impacts that occur at your site to decide whether they are financially viable in the long term.
Polymer bollards
In comparison, polymer bollards can cost a little more to buy than steel or concrete bollards, but the cost-savings in maintenance and upkeep mean they work out significantly cheaper in the longer term. The flexible and durable design means that even after repeated impacts, polymer bollards will still be intact and able to perform effectively.
Also, some polymer bollards, such as the ones by A-SAFE, are self-coloured and UV-stabilised as well as weather and water resistant, with a highly visible design. The means they don’t require repainting or additional anti-rust treatments. The only real maintenance they require is occasional cleaning which can be done with soap and water.
An investment in A-SAFE polymer bollards is a true investment in effective safety at your industrial facility. The long-term benefits and low-maintenance designs make them ideal for a one-off purchase that requires minimal upkeep, offering full peace of mind at busy sites. We can help find a solution that suits your budget – simply get in touch.
Concrete, steel and polymer safety bollards | A summary
While every type of bollard has its uses, when it comes to effective protection from site vehicles at factories, warehouses and industrial facilities, polymer bollards the ideal solution. They are extremely cost-effective and durable, while offering high levels of impact protection.